

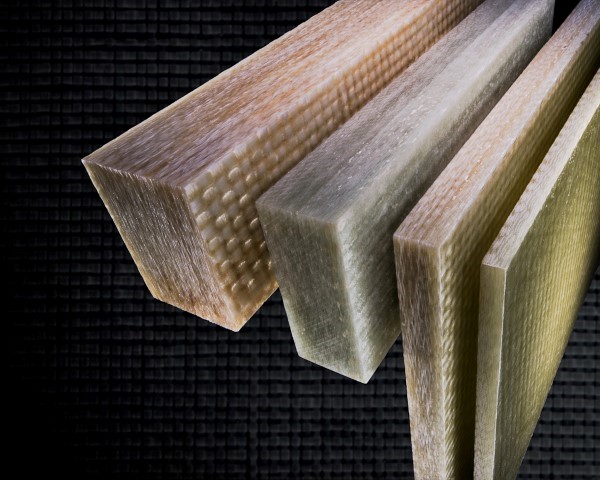
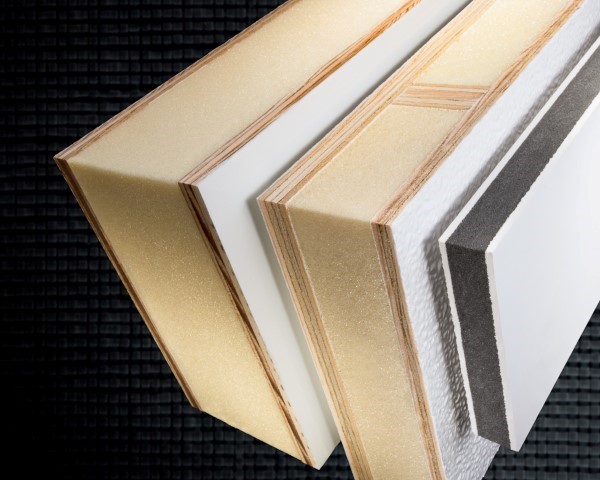
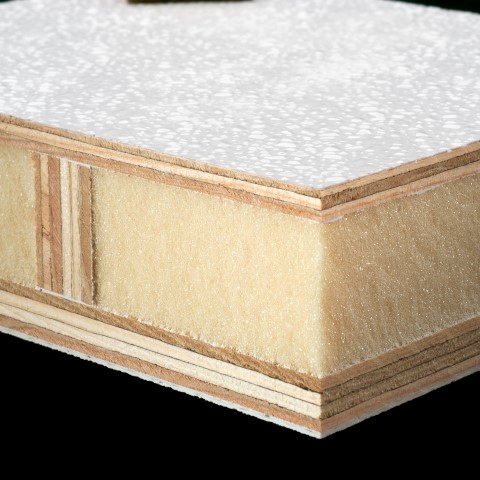
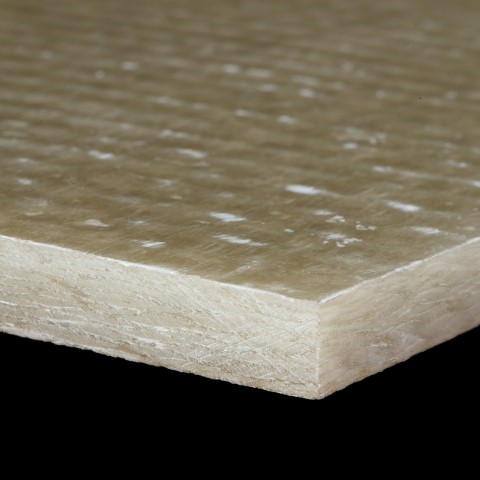
FRP Panels
Fiberglass Reinforced Panels (FRP)
Commonly called fiberglass reinforced plywood, fiberglass reinforced plastic, FRP panels, or simply FRP. Fiberglass composites have successfully been used in the transportation, construction, marine, military, and building industries since 1965. But only in the last 25 years have the unique qualities of FRP panels become better known, and the material more widely used in countless industries and applications.
Structural FRP Panels are Seamless, Durable, Strong & Abuse-Resistant
Our fiberglass panels are available in sizes up to 10 feet high by 58 feet long. Your choice of a variety of core materials are reinforced on each side by a fiberglass woven roving laminate which is then fused under heat and pressure to form a smooth, high gloss structural panel. The FRP panel interior is coated with a white polyester resin, interior continuous film, or gel coat finish, which provides a seamless surface that resists impact and abrasions from forklifts, pallets and shifting cargo. For transportation applications an interior scuff plate and/or multiple layers of fiberglass woven roving are available for additional reinforcement. This unique manufacturing process produces am FRP panel of uniform thickness that's attractive, extremely durable and weather resistant.
FRP Panels are easily maintained & repaired
Fiber-Tech FRP panels save maintenance time and cost because they do not pit or corrode like metals. These FRP panels are virtually unaffected by normal wear and tear. Fiber-Tech’s FRP panels are smooth, extremely attractive, and easily maintained. The standard gel coat exterior finish is quickly cleaned and is resistant to fading, yellowing or chalking
Most FRP damage can be easily repaired, and at considerably less cost than alternative components such as sheet/post, steel, and exotic metals. Fiber-Tech’s Maintenance & Repair Manual provides detailed, step-by-step identification and instructio for repairing damaged FRP panels.
Fiber-Tech’s Fiberglass Panel Technology
Successful fiberglass reinforced panel technology is based on several key componens, including:
- Core materials
- Resin formulation
- Fiberglass lamination schedule
- Exterior finishes
- Proven processes
Fiber-Tech’s success stems from our ability to combine the key components and proper materials to create the best FRP panels in the industry. We use our unique proprietary manufacturing process to build FRP panels which meet & exceed performance requirements for strength, durability, chemical resistance, and R-value.
All our fiberglass reinforced composite panels are built on custom designed and built manufacturing equipment. Our success has been our ability to combine the benefits from several types of fiberglass panel molding process into Fiber-Tech’s proprietary “Heat Accelerated Vacuum Assisted Infusion” process. Hundreds of million square feet of panels have been successfully built by Fiber-Tech using this proprietary process.
Liquid gel coats are sprayed, fiberglass woven roving, mats, and veils are rolled into place and saturated with the proper amount of evenly distributed resin chosen specifically for the fiberglass panels end-use. The process is repeated on both sides of a core material and then the panel is cured under heat and vacuum to create the industry’s largest structural fiberglass panel.
Fiber-Tech’s proprietary fiberglass FRP panel manufacturing process provides a wide variety of benefits which are continually being enjoyed by our thousands of customers we have supplied for over forty years.
Contact Fiber-Tech for FRP Panels Today
Don’t settle for glued skin-to-core panels produced by other laminators. You can have a custom manufactured structural fiberglass panel built specially for you which meets all of your requirements – allowing your product to also exceed your customer’s expectations. Call to learn more about our wide variety of FRP panels to perfectly fit your project requirements and panel needs.
Call the “Composite Panel People”at Fiber-Tech Industries today!